Job Hazard Analysis
Problem: A Serious Workplace Accident
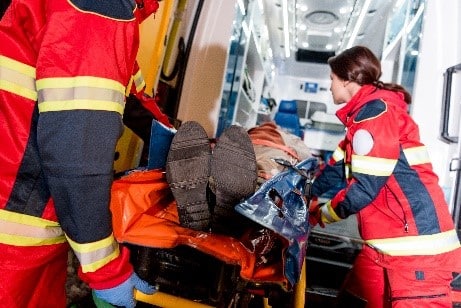
Your Problem: One of your employees has just suffered a serious workplace accident. It’s not like there weren’t warnings: several workers have had minor injuries over the past few months while performing the same task. You know you need to make a change to prevent more employees from ending up in the hospital. But how?
Your Solution: Conduct a Job Hazard Analysis (JHA). What is a JHA? It’s an exercise in detective work that seeks to identify uncontrolled workplace hazards before they result in an injury or illness.
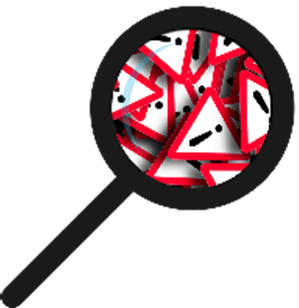
The goal is to discover:
- How can the hazard(s) be controlled?
- What could go wrong?
- What are the potential consequences?
- How could it arise?
- What are other contributing factors?
- How likely is it that the hazard will occur?
JHAs focus on the relationship between the worker, the task, the tools, and the work environment. For this reason, it is very important to involve your employees in the hazard analysis process. Involving employees will help minimize oversights, ensure a quality analysis, and get workers to share ownership in their safety and health program.
While all affected employees should be involved, a designated competent person will need to lead the JHA.
Make It Happen: Proactively mitigate hazards and foster a safer work environment in six essential steps.
Step 1. Select and Prioritize Jobs to Analyze: Focus on jobs with frequent or severe injury potential. Gather input from workers, review injury records, and consider new or recently changed jobs.
Step 2. Analyze Job Steps: Observe different workers performing the task and break it down into steps. Communicate the purpose to workers to reduce concerns and verify the steps with multiple employees. Photos or videos can help.
Step 3. Identify Hazards: Examine each job step for potential hazards, considering past incidents and worst-case scenarios. Start with the most obvious and common risks, like falls, electrical, struck-by, and caught-between hazards, but don’t overlook less noticeable risks, such as chemical, mechanical, and ergonomic hazards.
Step 4. Describe Hazards: For each hazard, describe the environment, exposure, cause, potential consequence, and contributing factors.
Step 5. Select, Install, Maintain, and Review Controls: Modify job steps to eliminate hazards where possible. If not, use the hierarchy of controls to protect workers. Once controls are implemented, review them with workers, gather feedback, and monitor for any attempts to bypass controls.
Step 6. Review Your Job Hazard Analysis: Reassess the JHA after job changes, incidents, or periodically to ensure it remains accurate and continues to identify hazards effectively.
Next Steps: Train your employees on the new procedures you establish after concluding your JHA. Make sure they know how to perform the task safely and monitor them to ensure that they actually follow procedures.